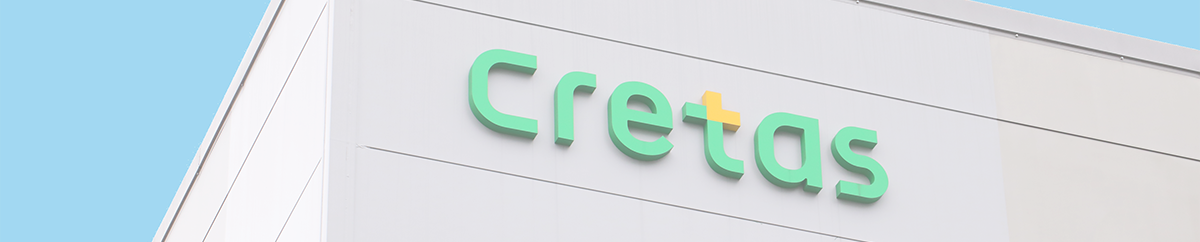
樹脂加工RESIN PROCESSING
射出成形
樹脂の成形加工で主に用いられる材料は、細かい粒状のペレットと呼ばれるものです。
同じ形状のものを大量に生産にするのに優れた加工方法です。
成形加工にはいくつかの種類があります。このページでは、射出成形についてご紹介します。
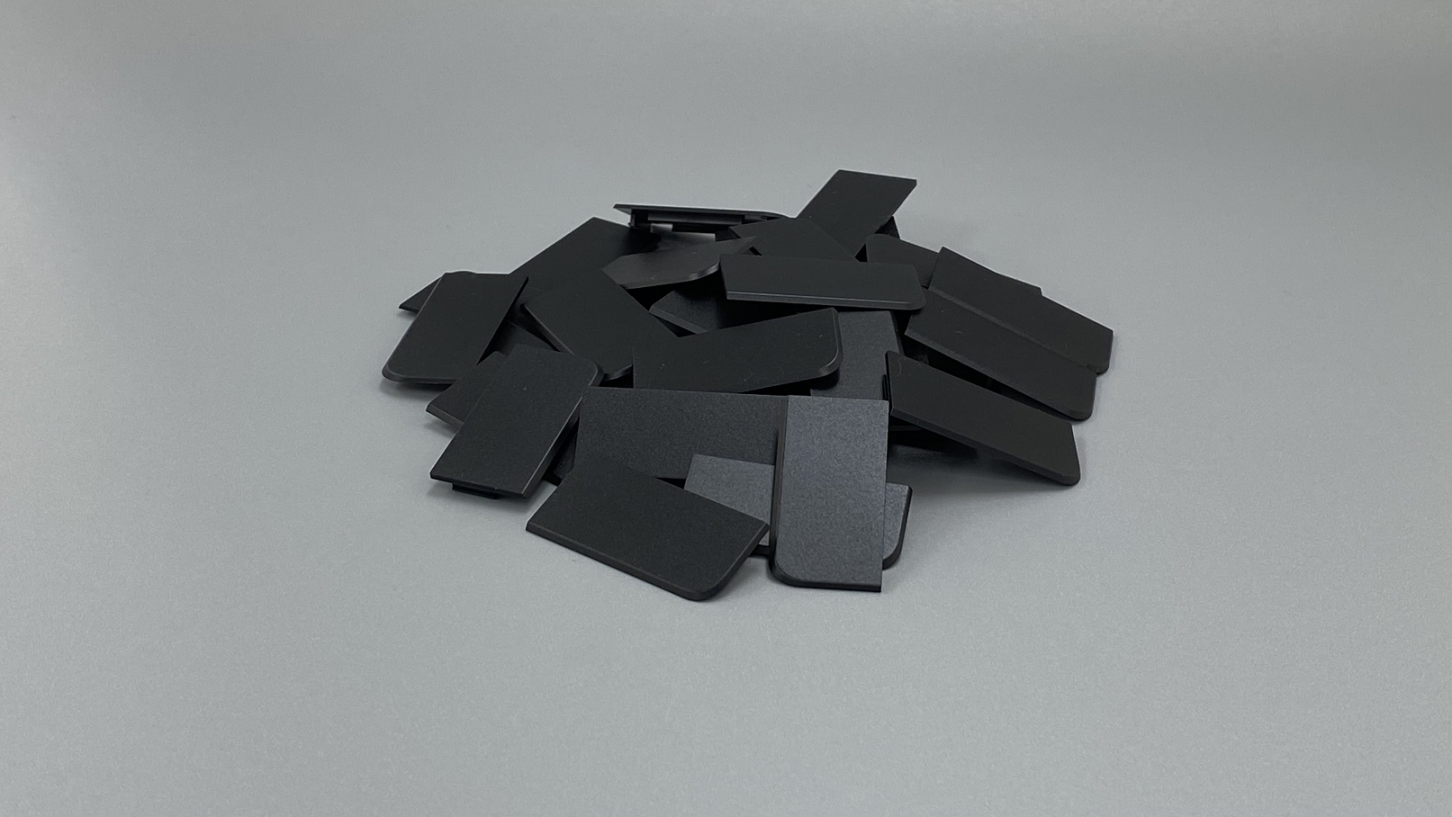
◆射出成形加工とは
射出成形とは、加熱して液状になった樹脂材料を金型に注入し、冷やし固めて成形する加工方法です。
注射器のように圧力をかけて細い部分に材料を送り込む様子に似ていることから、「射出成形」と呼ばれるようになりました。
機械による自動化が進んでおり、生産数が多いほど製品1個当たりのコストを抑えることができるメリットの反面、成形金型を作らなければならないため、初期費用(イニシャルコスト)として高額な金型製作費が必要となってしまうデメリットもあります。
金型製作は、製品形状や取り数(1つの金型で何個分作るか)により、その費用と製作時間は大幅に変わります。
金型の製作時間が数ヶ月に及ぶことも、そう珍しいことではありません。
また、金型の保管にそれなりの場所を必要としますので、保管料が掛かってしまったり、加工の度に成形メーカーから返却されて自社で保管を行わなければならないケースもあります。
複雑な形状を含め様々な形の製品を、高い精度で素早く大量に生産することができるので、大量生産に向いている製造方法です。
家電の外装部分や食器、文具類などの日用的に使用されているプラスチック製品の多くが、この方法で製造されています。
◆射出成形の工夫
射出成形では金属部品を金型にセットして、樹脂と金属を一体化させた加工品を作ることも可能です。
このような加工は、インサート成形と呼ばれており、例えば製品にナットやボルト、板金を取り付けたい場合などで適用されています。
後加工で部材を取り付けるよりも、簡単に生産することが出来るのがメリットです。
その他、金型製作における工夫としては、金型にシボ加工を施しておくことで、表面にシボ付きの製品を作ることもできます。
この方法であれば、成形後に追加加工として表面処理を施す必要がなくなります。
また、金型を作る際に複数の製品を作れるように設計することも可能です。
一番イメージをしやすいのは、プラモデルのパーツになるかと思います。
複数取りの金型を設計すれば、一回の成形で複数個を生産できたり、数種類の部品を同時に生産できるようにすることもできます。
よくあるパターンとしては、左右対称部品を同数作りたい場合が挙げられます。
それぞれの部品ごとに金型を作るよりも、金型費を抑えられるだけでなく、複数個を一回で成形することで製品コストも下げられるというメリットがあります。
ただし、その金型を使用して複数個の内、どれか1つだけ作ることは難しくなってしまうデメリットが生じます。
金型の構造次第では可能な場合もありますが、金型に負荷が掛かってしまうので、金型の寿命を短くしてしまう可能性があります。
◆成形用語
成型加工品の図面に記載されていたり、成型加工工場との打ち合わせで頻繁に使われる成形不良を表す用語に焦点をあてて、いくつかご紹介します。
射出成形時によくみられる現象として代表的なものに、ウェルドラインやヒケ、ボイド、バリ、反り、ねじれ、黒点などがあげられます。
製品設計時の注意点としては、アンダーカット形状が挙げられます。
成形時に金型内に流れる樹脂が合流した際に発生する線状の模様です。
完全になくすことは、できない為、意匠面で使用する部品では、見栄えの問題となることがあります。
成形後、樹脂が冷えて固まる際に、樹脂が収縮し、製品の表面に凹みが発生してしまうことがあります。
その凹みの事をヒケと呼びます。成形後、樹脂は空気に触れている表面から固まっていきます。
一方、内側はまだ熱を持っていて、表面より遅れて固まっていきますが、その際に、内側の収縮に引っ張られて、
表面がヒケてしまいます。形状によっては、反りやねじれが生じることもあります。
製品の肉厚な部分程、収縮が大きくなり、大きなヒケとなることがあり、製品設計時に要注意となります。
ヒケと同様に成形後の樹脂の収縮や、材料の水分や発生するガスによって、中に気泡のような空洞ができることがあり
ボイドと呼んでいます。材料の色次第では、外観では判断することは出来ません。
対策としては、成形条件や材料を十分に行うことで、改善が見込まれます。
透明や白色の製品などは、顕著にみられる現象です。樹脂を溶融するシリンダーの中で、樹脂が炭化してしまい細かい粒状の物質が出来てしまい、
製品成形時に製品表面に現れることがあります。シリンダー内の樹脂をパージしたり、スクリューを分解し清掃を行うことで改善が見込まれます。
成形時後に金型から取り外しができなくなる形状の事です。
製品の形状や、金型の設計にもよりますが、「ひょうたん」のような形状をイメージして頂くと分かりやすいかもしれません。